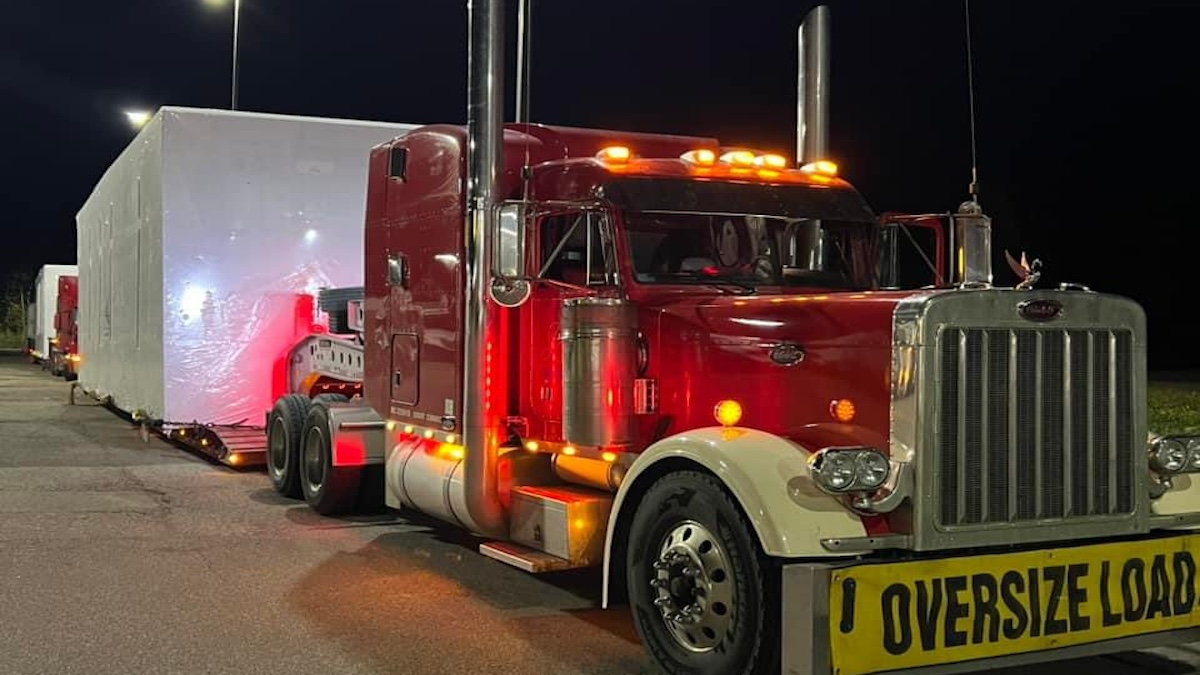
The Future of Modular Construction in Industrial Applications
The construction industry is undergoing a significant shift, thanks to modular construction. This approach involves building standardized components or “modules” in an off-site factory and then assembling them on-site.
For industrial applications, this technique offers a new level of flexibility, speed, and control that traditional construction simply can’t match. As global industries face tighter project timelines, skilled labor shortages, and demands for greener infrastructure, modular construction is quickly becoming a preferred choice.
What Is Modular Construction in the Industrial Sector?
Definition and Basic Principles
Modular construction in industrial settings refers to the prefabrication of structures or systems in controlled environments, often far from the job site. These modules can range from small utility rooms to entire sections of production facilities, complete with mechanical, electrical, and plumbing systems already installed.
After being manufactured, these modules are transported to the construction site and connected to form a fully functional structure. Unlike temporary or mobile buildings, modular structures are permanent and built to meet conventional codes and standards.
Common Industrial Applications
Modular construction is widely used across industries where efficiency, reliability, and scalability are critical. Applications include:
- Data centers with rapidly deployed IT infrastructure
- Oil and gas processing facilities requiring high-precision skids
- Power generation plants
- Automotive and semiconductor manufacturing
These sectors demand consistency, fast delivery, and adaptability—all of which are inherent strengths of modular construction.
Current Benefits of Modular Construction in Industrial Projects
Speed and Efficiency
In modular construction, site preparation and module fabrication happen simultaneously. This parallel workflow can reduce total construction time . For industrial projects where delays mean lost revenue or missed market opportunities, this speed is a game-changer.
Cost Predictability and Budget Control
Because modules are built in a controlled factory environment, costs become more predictable. There’s less exposure to weather-related delays, labor shortages, or site logistics issues. Bulk procurement of materials and streamlined scheduling also help reduce waste and improve cost efficiency.
Safety and Quality Control
Safety is a top concern in industrial projects. Factory-based manufacturing environments are easier to monitor and control, resulting in safer working conditions. At the same time, quality control is more consistent, with inspections and tests conducted throughout the fabrication process.
Sustainability and Environmental Impact
Modular construction significantly reduces waste—materials are reused, and excess inventory is minimized. There’s also less on-site disruption, which is beneficial in environmentally sensitive or densely populated areas. Moreover, many modular components are designed with energy efficiency in mind, aligning with ESG and green building goals.
Emerging Trends Shaping the Future of Modular Industrial Construction
Customization with Standardization
One of modular construction’s unique advantages is its ability to offer customized solutions within a standardized framework. This mass customization allows for flexibility without compromising speed or cost efficiency.
Sector-Specific Innovations
Modular Solutions for Data Centers
The growth of cloud computing and AI is driving demand for data centers that can be deployed quickly and scaled easily. Modular data centers are shipped with integrated cooling, power, and server infrastructure, making them operational within weeks instead of months. Their predictable performance and rapid deployment make them ideal for edge computing and remote locations.
Modular Clean rooms in Pharma and Healthcare
Pharmaceutical manufacturing requires highly controlled environments. Modular clean rooms are built to meet ISO and GMP (Good Manufacturing Practices) standards, offering consistent quality with faster delivery times. These clean rooms can also be relocated or reconfigured, which is valuable during emergencies like pandemic response or sudden production increases.
Modular MEP and Utility Skids
Mechanical, electrical, and plumbing (MEP) systems are often complex and labor-intensive to install on-site. Modular skids—self-contained systems with pre-integrated equipment—eliminate this challenge. Once delivered, they are simply hooked up to the building’s main systems, reducing downtime and installation errors.
Challenges and Limitations
Design Constraints
The size and shape of modules are limited by transportation and lifting equipment. Oversized units may require special logistics planning, permits, or even breakdown into smaller sub modules, which can affect cost and scheduling.
Regulatory and Permitting Barriers
Modular construction sometimes faces delays due to unfamiliarity among local regulators. Code compliance across jurisdictions is not always straightforward. Companies must engage with permitting authorities early in the process to avoid unexpected roadblocks.
Industry Resistance to Change
Many stakeholders in industrial construction—engineers, project managers, or contractors—are accustomed to traditional workflows. Shifting to a modular mindset requires training, cultural change, and new partnerships. However, as more success stories emerge, the industry is slowly embracing this evolution.
The Role of Modular Construction in Future-Ready Infrastructure
Resilience and Scalability
Modular buildings are inherently resilient. Damaged components can be quickly replaced, and additional capacity can be added by simply integrating new modules. This is especially useful in fast-changing industries or in disaster-prone regions where infrastructure needs to bounce back quickly.
Global Supply Chain Resilience
In a post-pandemic world, supply chain delays and international shipping constraints have made modular construction even more appealing. It enables localized manufacturing of building components, reducing dependence on long-distance supply chains and allowing for quicker response to demand.
The Road Ahead – Predictions and Strategic Recommendations
Future Demand Outlook
The global modular construction market is projected to exceed $100 billion in the coming decade, with industrial applications taking a significant share. This growth is driven by increasing demand for quicker project delivery, labor efficiency, and sustainable building practices.
How Industry Leaders Can Prepare
To capitalize on this momentum, industrial companies should:
- Integrate modular thinking early in project planning
- Choose partners with modular expertise and proven track records
- Train internal teams in modular project management
- Invest in digital tools that support modular workflows
Forward-thinking organizations that embrace these steps will be better positioned to deliver high-performance facilities faster and more efficiently than ever before.
Conclusion
Modular construction is not just a passing trend—it’s the future of industrial development. As industries grow more complex and global markets demand agility, modular solutions provide the speed, quality, and innovation needed to stay ahead.
At Miller Industries, we’ve been at the forefront of this transformation. Our team specializes in designing and delivering high-quality modular systems tailored to the unique needs of industrial clients. From conveyor systems and structural steel platforms to MEP modules and powder-coated enclosures, we understand what it takes to build smarter, faster, and stronger.
If you’re planning your next industrial project and want to explore how modular solutions can give you a competitive edge, we’re here to help. Visit www.millc.com to learn more about how Miller Industries can bring your vision to life.
FAQs
What industries benefit most from modular construction?
Industries like data centers, oil and gas, pharmaceuticals, manufacturing, and power generation benefit greatly due to the need for fast deployment, flexibility, and precision.
How does modular construction reduce downtime in industrial projects?
Since modules are built off-site while site preparation happens in parallel, the overall construction time is significantly reduced, minimizing operational disruptions.
Is modular construction more sustainable than traditional methods?
Yes, it reduces material waste, improves energy efficiency, and causes less disruption at the construction site—all of which contribute to a smaller carbon footprint.
Can modular buildings be expanded or modified later?
Absolutely. One of the strengths of modular construction is its flexibility. Buildings can be expanded or reconfigured easily by adding or removing modules based on changing needs.
How cost-effective is modular construction compared to traditional methods?
While upfront design and manufacturing costs may be slightly higher, modular projects often save money through reduced labor needs, shorter build times, and minimized site delays.
Can modular buildings be relocated or repurposed?
Yes. One of the unique advantages of modular construction is the ability to dismantle, relocate, or repurpose modules as operational needs change.
What materials are commonly used in industrial modular construction?
Steel, aluminum, and high-quality composite panels are widely used due to their durability, structural strength, and ability to withstand heavy industrial use.
How does modular construction affect worker safety?
Off-site fabrication reduces exposure to hazardous site conditions, heavy machinery, and weather risks, significantly improving worker safety.
Are modular structures as durable as traditional buildings?
Yes, when designed to code and properly maintained, modular structures are equally durable and often built with tighter quality control in factory settings.