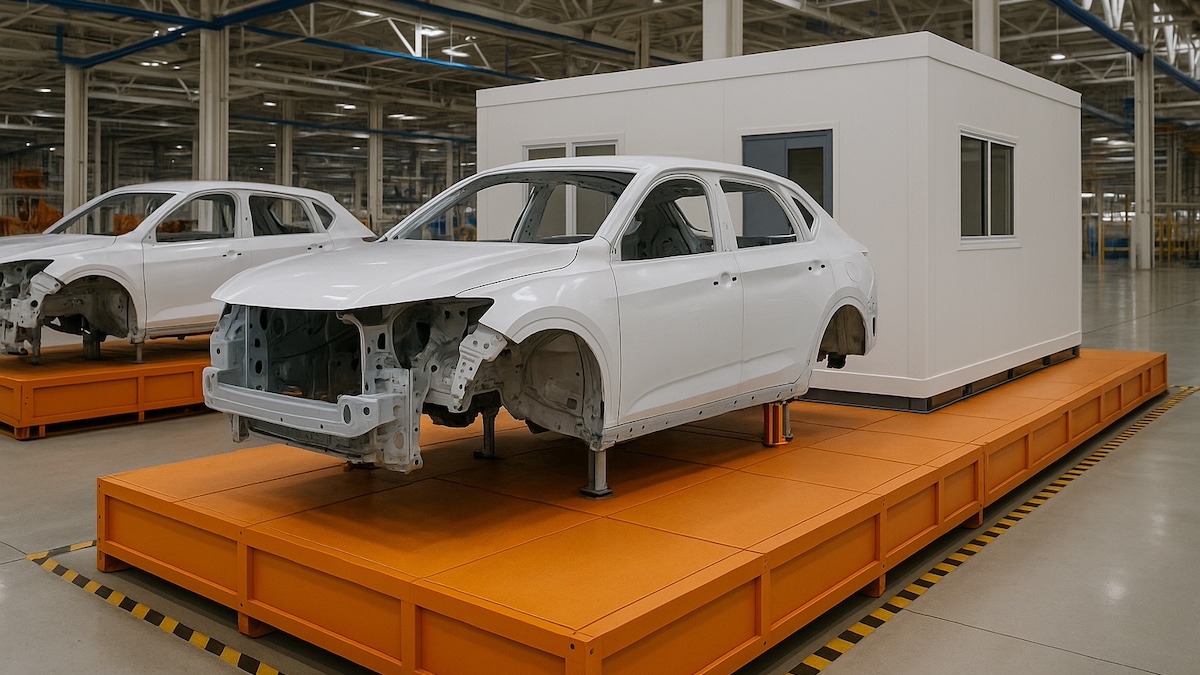
The Role of Modular Construction in Automotive Manufacturing Plants
As the automotive industry continues to rapidly evolve at high speeds—driven by innovations like electric vehicles (EVs), automation, and sustainability—manufacturers are under pressure to adapt quickly.
From retooling facilities to launching entirely new production lines, speed and flexibility have become essential. Enter modular construction, a game-changing approach that allows automotive manufacturers to rapidly expand or upgrade their facilities while maintaining production efficiency.
In this guide, we explore how modular construction is transforming automotive manufacturing plants, improving timelines, lowering costs, and providing the adaptability needed to stay competitive.
What Is Modular Construction?
Definition and Core Principles
Modular construction is a building method that involves fabricating modules or entire components of a structure off-site in a controlled environment, then transporting and assembling them at the final location. This method contrasts with traditional construction, where everything is built on-site from the ground up.
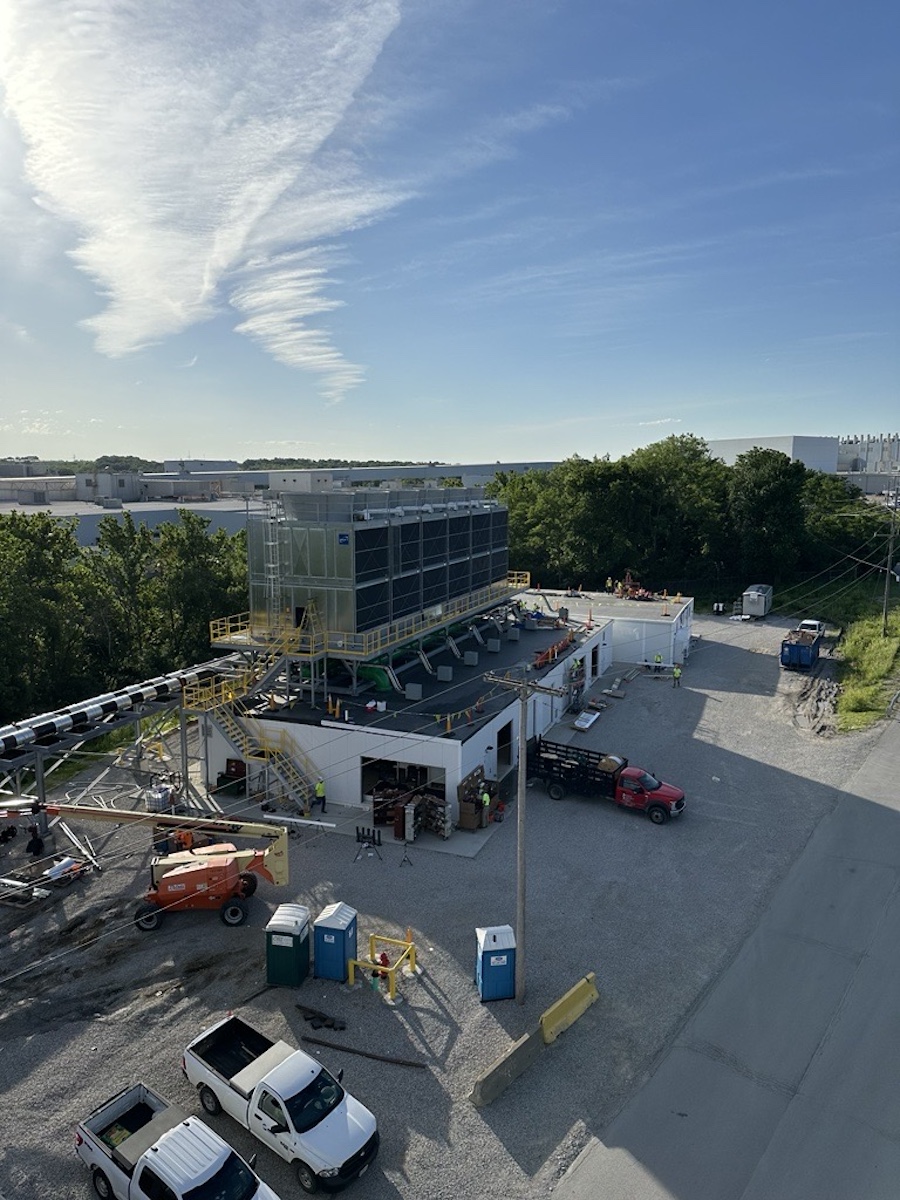
Key principles include:
- Prefabrication of components in a factory setting
- Parallel workflows, enabling site preparation and module construction to happen simultaneously
- Efficiency and quality control due to standardized processes and controlled environments
Types of Modular Systems
- Permanent Modular Construction (PMC): Long-term solutions integrated into the final structure, like control rooms or HVAC enclosures
- Relocatable Modular Construction (RMC): Temporary structures that can be moved or repurposed—ideal for rapidly changing production environments
- Hybrid Modular Systems: A combination of both, customized to suit the specific needs of a plant
Why the Automotive Industry Is Adopting Modular Construction
Accelerated Construction Timelines
Time is money in manufacturing. Traditional construction methods often cause production delays, especially when reconfiguring facilities. With modular construction:
- Modules are built while the site is being prepared
- Weather-related delays are minimized
- Commissioning and installation are significantly faster Result: faster project completion and quicker time-to-market for new products
Cost Savings and ROI Benefits
Modular construction can deliver significant cost advantages:
- Reduced labor costs from shorter construction periods
- Minimized operational disruptions for existing plants
- Lower materials waste due to factory-controlled processes In an industry where margins are razor-thin, every cost saving improves return on investment
Scalability and Flexibility
Automotive manufacturing facilities often need to adapt to changing product lines, whether it’s for launching an EV variant or integrating new automation. Modular systems make this easy:
- Add or remove production modules as needed
- Reconfigure the layout with minimal impact on operations
- Scale up or down with future-proof infrastructure
Improved Quality and Safety
Prefabricated modules are built in highly controlled environments, reducing:
- Construction errors
- Material waste
- On-site accidents The result is a safer, cleaner, and more efficient build process for automotive plants
Applications of Modular Construction in Automotive Plants
Modular construction isn’t limited to building exteriors—it supports a wide array of internal plant systems
Modular Offices and Control Rooms
- Installed during renovations or new builds
- Ready-to-use spaces with integrated electrical, HVAC, and data systems
Utility Infrastructure
- Electrical switch rooms, boiler plants, Chiller plants, and air handling units (AHUs) housed in modular enclosures
- Helps keep critical systems separated from production areas for better maintenance and safety
Stairs, Platforms, and Mezzanines
- Modular steel structures designed for easy access to machinery or elevated workspaces can be built off-site and quickly installed
- these steel structures are safety-optimized and built to spec
Challenges and Considerations
While modular construction offers several benefits, some challenges must be navigated.
Design Coordination with Plant Engineering
- Early engagement with OEM plant engineers is essential
- MEP (mechanical, electrical, plumbing) integrations must be planned in detail
Transportation and Logistics
- Large modules require specialized transport and may face logistical constraints
- Local site access and permits must be considered
Customization vs Standardization
- Standardized modules are cost-effective but may limit customization
- A hybrid approach often balances uniqueness and efficiency
Future Outlook
As sustainability, speed, and adaptability grow in importance, modular construction is becoming a critical enabler of modern automotive plant design
FAQs
Is modular construction suitable for all areas of an automotive plant?
While not ideal for every structure, modular solutions can be used for most internal spaces—like mezzanines, and utility infrastructure.
How does modular construction reduce downtime in existing plants?
Modules are built off-site, so installation happens quickly with minimal on-site disruption. This ensures continuous operation during upgrades.
Can modular construction support green building certifications like LEED?
Yes. Modular builds reduce waste, promote energy efficiency, and often contribute to LEED certification due to controlled construction practices.
How long does it take to implement modular systems in an automotive plant?
Depending on complexity, modular systems can be implemented in as little as 4 to 10 weeks, significantly faster than traditional construction timelines.
Conclusion: Engineered for Performance. Backed by Miller Industries.
At Flex Air, a division of Miller Industries, we’re dedicated to powering the future of automotive manufacturing through custom modular HVAC and air handling solutions. Our systems are engineered to meet the high standards of today’s production environments—delivering the speed, reliability, and adaptability that modern plants require.
From clean rooms to paint booths and modular control centers, Flex Air partners with engineers and builders to provide flexible, scalable systems that keep your operations running efficiently. Backed by the strength and expertise of Miller Industries, we’re here to help you build smarter, breathe easier, and move faster.
Let’s shape the next generation of automotive manufacturing—together.